Luke Workman is a complete maniac. He’s also one of the world’s leading lithium battery pack designers for electric vehicles, and he’s come up with a revolutionary battery design that he says could bring on clean, quiet, long-distance, commercial-scale supersonic airliners.
The latest generation of electric powertrain technology is leading toward some very exciting developments in the aviation world, from VTOL air taxis to potential flying car designs. But the airline industry is still roughly as slow, and noisy, and expensive, and inefficient and dirty as it has been for the last 40 years – and we haven’t seen much from the electric world yet to challenge it.
The trouble isn’t the motors – electric motors should be extremely effective in the air, since they work well at low-drag high altitudes, where the air is thin enough to cause problems for combustion engines.
The main problem, as everyone knows, is batteries – getting enough energy into a light enough package to deliver a useful range. And that’s where wild-man EV battery pack guru Luke Workman figures he’s got a solution.
If you haven’t read our fun multi-part interview with Luke Workman before, suffice it to say he’s a unique and wonderful character with his fingers in a remarkable number of electric vehicle pies. From electric motorcycles to tilt-rotor VTOL aircraft and a growing list of other applications, he’s designed some of the most rugged and high-density lithium battery packs in the business. These days as a freelance consultant, he’s regarded as one of the world’s best lithium battery designers.
Now, he believes he’s worked out a unique battery design that could open the door to long-range, supersonic, electric aviation on a commercial scale – proper airliner-size beasts. And, he says, it can be done using existing battery chemistry; no need to wait for any of the technology leaps that the mainstream car and motorcycle industries are holding on for.
How? Well, existing batteries carry a lot of extra weight in support materials. “About 35 percent of the weight in the cell is current collection, sheets of aluminum and copper foil that are just there to get the energy in and out of the cell,” says Workman. “That’s a lot of weight that’s not active material. It’s a lot of weight a plane has to carry that’s not storing energy.”
Take this pouch cell, for example. The foil tabs on the top are the bits that interconnect current for the circuit. There’s 20 layers of aluminum foil for the positive terminal, 20 layers of copper for the negative. Those foil layers extend down right through the cell, and they need to be 20 layers thick so they can carry the full current of the cell up to that top tab, which joins with the tabs of the other cells to make a series.
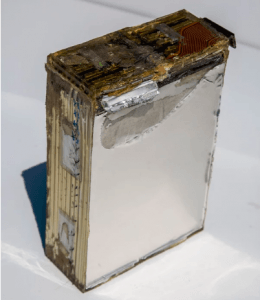
That’s a very efficient way to package a battery for most uses. In fact, this ripped out battery, from a Zero electric motorcycle, has a higher energy density than anything else on the market at around 161 usable watt-hours per kilogram of battery, fully packaged. But that’s a long way short of the 400-500 watt-hours per kilogram it’s going to take to achieve serious long-range high-speed passenger airliners.
“But here’s the trick,” says Workman, “I’ve come up with a battery design that weighs far less and handles heat insanely well – it just requires a gigantic, flat surface area. Like, say, the oversized wings of a supersonic plane.”
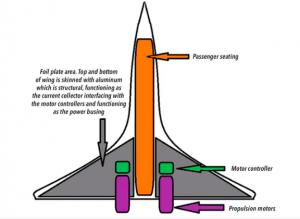
This isn’t about using the area inside the wing or fuselage to store battery cells. Workman’s idea is to use the whole wing surface as part of a giant battery. “I wanna use the full available wing area for electrode plate surface, and conduct through the axis with the cross section of the full wing area.”
Instead of conducting energy out through the tabs on top of the cells, Workman wants to sandwich huge sheets of active material together between super-thin double-sided foil layers – one side aluminum, the other copper. This way the entire cells are basically in contact with one another, conducting through their whole surface plane, instead of out through tabs.
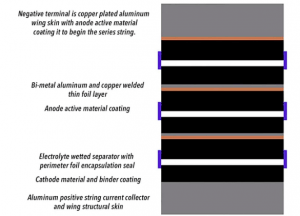
“Composite structures, to be strong, need a middle portion there to support the skin on the outside,” says Workman, “We can use the battery as the middle layer of the wing, and we can use the aluminum skin of the wing as a current collector to get power from the ends of that battery sandwich out to the motors.”
“There’s a way to conduct that’s the hard way, and a way that’s incredibly easy, with abundant conductivity. In today’s small batteries, we conduct the hard way, because it’s the only way we can make high capacity, high power cells at that scale. This sandwich idea couldn’t work at the small scale, because you couldn’t get it up to a decent capacity.
“But give me an entire supersonic aircraft wing, and that problem just goes away. That huge surface area of conductive material would conduct extremely efficiently while generating almost no heat. And because there’s almost no heat to deal with, we could use higher density active materials that we can’t use in the automotive world.”
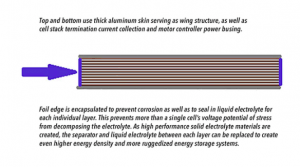
Doing this for a small plane, a car or a motorcycle doesn’t make sense. But once you’ve got a Concorde-sized, big flat wing to work with, the math starts to work out. “From quick estimations based off existing cell materials that are safe and have high cycle life, you can get around 13,300 amp hours per 0.2 mm of thickness for each foil layer. Nine-hundred layers would give us 3.3 kV nominal and around 44 megawatt hours of battery storage.
“Total weight would be roughly 104,000kg, with an extraordinarily high percentage of that mass being active material, and lower conduction losses than any currently existing topology despite its high charge/discharge rate capabilities. That gives us 423 watt hours per kilo, well and truly in the ballpark, using proven materials we can get off the shelf today. And that’s if we’ve got 300 square meters of wing area, with a foil core about 20cm thick and 1cm current conductor plates on the top and bottom. The bigger this battery gets, the more efficient it becomes.”
That means the bigger the plane gets, the further it’ll be able to fly, and the more efficient it’ll get at carrying cargo or passengers. And if there’s enough surface area, it could be equally useful on large scale electric boats, or for grid level power storage.
Getting rid of packaging and those thick tabs that interconnect the cells in a regular battery can save a meaningful amount of weight on a large scale battery. But it’s the low impedance, low resistance conductivity path and reduction in voltage sag and heat production that lets you really ramp up the capacity of the thing and increase charge rates.
So what’s going to happen with the idea? “I’m not going to build this personally,” says Workman, “not unless it was the only project I was working on. If any company wants to use it, they’re very welcome to and I’m happy to help.”
Workman isn’t the type to believe in intellectual property –he’s far more interested in making decisions that benefit the planet. “The reason I’d never restrict anyone from using this is that we’re all sharing the same spaceship here. We either do the things we need to do to keep an atmosphere on this planet, or we fail the Darwin test as a species.”
The sooner we get zero-emissions electric airliners out into the market, the sooner we can let our fleets of heavily polluting 747s and Airbuses fade into obscurity. And they will. Electric aviation will be a fraction of the cost of fossil fuel flight, both in terms of fuel and maintenance costs. The aircraft will be much quieter, and trips will be significantly shorter with high altitude supersonic speeds.
Battery-powered airliners are coming, whether by virtue of several generational leaps in battery chemistry, or by the use of radically different packaging technology like this. We’ll keep an eye on this one, hopefully somebody will pick it up with the resources and the drive to make it happen.